
Modern factories and industrial plants are extremely complex operations with many moving parts. Getting optimal performance requires paying attention to details that may not seem important at first glance. The experts over at Blues IoT say that by focusing on a few key areas, manufacturers can unlock powerful improvements in their plant efficiency, sustainability and bottom line.
In the following paragraphs, we will explore some less obvious ways to boost productivity by tapping into the industrial internet of things and other modern technologies.
Fine-Tuning Equipment Maintenance
The machinery and equipment that fill factories and plants are the heart of operations. Keeping these assets in top working condition is essential, but maintenance plans typically focus just on preventing outright failures and breakdowns. Taking maintenance efforts to the next level by fine-tuning equipment for peak energy efficiency can generate massive long-term payoffs.
Upgraded machine monitoring tools offered by the industrial internet of things give operators granular insight into things like internal friction, temperatures, and vibration. Tiny changes and tweaks found through analysis of this data might increase energy efficiency by 3-4%. That may not seem like much, but across an entire facility with hundreds of machines, the compounding savings add up in a big way while also boosting equipment lifespan.
Optimizing Energy Use Patterns
Industrial energy use follows patterns shaped by production schedules, breaks, seasonal changes and other factors. Failing to align energy supply properly with anticipated demand leads to waste through things like keeping equipment idling when not needed.
New automated systems can forecast energy needs down to a very precise level and orchestrate just-in-time delivery of power.
As an example, a plant may be able to briefly turn off certain banks of lights right before a planned production break when that part of the facility will be vacant, or chillers and cooling systems can cycle on and off more tightly based on changing weather conditions. This kind of optimization requires a holistic view of operations, but it can drive energy efficiency up substantially without capital investments.
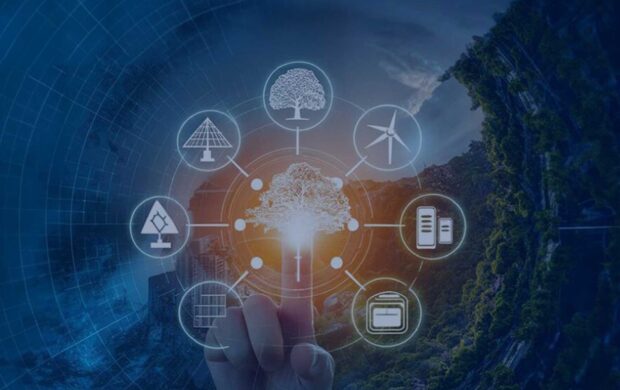
Enhancing Material Flows
To manufacture products, a steady flow of raw materials, components, and subassemblies needs to continuously enter and move through a plant. Inefficiencies anywhere along that pathway diminish productivity and boost waste. Smoothing out kinks in material flows means manufacturers can realize better process optimization.
Careful analysis often reveals bottlenecks where materials temporarily pile up waiting to advance to the next step. Addressing these constraints through things like modified lot sizes, storage buffers or staggered schedules helps maintain constant motion.
Another approach is closely integrating suppliers and inventory management via logistics data sharing platforms. Having tighter control over when and how much material gets delivered based on real production demand minimizes situations where parts shortages or overages stagnate flows within the plant itself.
Leveraging Building Design Elements
A factory or plant’s physical structure seems like an unchangeable aspect, but relatively simple upgrades to things like insulation, windows, roofing, doors and ventilation can have a measurable impact. Gaps or inferior materials lead to higher heating and cooling expenses being required to maintain employee comfort and ideal working conditions.
New spray foam insulation products provide better seals around ductwork, attics, walls and ceilings than traditional batt insulation. High-tech low-emissivity window coatings limit heat transfer far better than ordinary glass. Composite roofing materials like ethylene propylene diene terpolymer rubber resist weather, rot, mold, and insects better than wood or asphalt alternatives. Attention to details like this improves the building envelope’s natural efficiency at retaining desired temperatures.
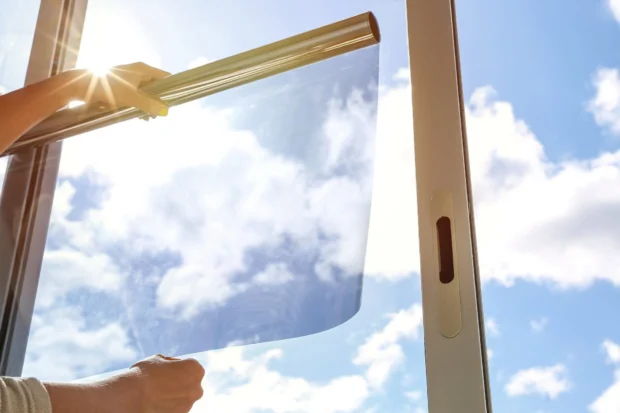
Capturing Waste Heat, Steam and Gases
Depending on the specific industrial processes involved, considerable energy often gets literally dumped straight into the air through waste heat, steam, gases, and vapors. Diverting some portion of these byproducts to be repurposed on-site instead of being wasted can significantly augment overall plant efficiency.
Heat recycling technology has advanced to the point where capturing and reusing at least some waste thermal energy is feasible for many facilities through things like heat exchangers. Condensing and redirecting escaping steam or gases to be productively used elsewhere on-site cuts waste while reducing external energy inputs needed to power heating equipment. The viability varies widely based on particular industrial operations and requirements, but it is always worth exploring.
Improving Water Usage
Water plays a major but sometimes invisible role in plant operations for things like cleaning, cooling machinery and climate control systems. Reducing unnecessary water usage through small, targeted changes not only saves directly on utilities, but also cuts the embedded energy needed to supply that water.
Fixing simple leaks and drips can yield surprisingly big savings on both water and energy bills. Switching to more efficient nozzles, valves, condensers, and other water-based equipment compounds those savings further, and installing systems to capture, treat and reuse gray water on-site rather than paying for complete external water purification reduces waste even more.
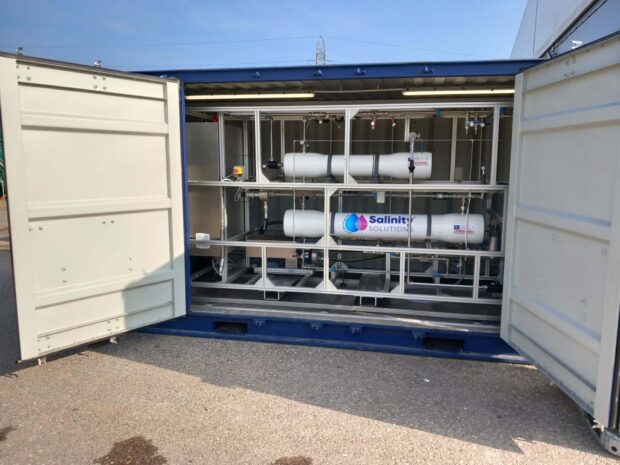
Empowering Employees
Ultimately, a factory or plant’s frontline employees have the biggest day-to-day impact on efficiency. Engaged, motivated workers who fully understand the role they play in optimizing operations can drive powerful bottom-line improvements through their individual actions.
Programs aimed at both educating and incentivizing conservation behaviors among employees enable huge aggregate results. A plant where machinery only runs when truly needed, lights stay off in vacant rooms, leaks get reported promptly and everyone contributes ideas pays dividends across the board. Combining enriched employee engagement with targeted technology upgrades unlocks the full potential of a facility.
Conclusion
Boosting a factory or industrial plant’s total efficiency requires looking beyond the usual metrics of machine capacities and production volumes per hour.
Paying attention to ancillary factors like equipment maintenance practices, energy management systems, building envelope design attributes, waste stream capturing capabilities and employee engagement programs means operators can find powerful new opportunities for improvement.
Tapping into the emerging possibilities of the industrial internet of things opens a deeper well of hidden optimization potential that delivers outsized efficiency gains without necessarily investing in brand new machinery. Prioritizing some of these less obvious elements reveals new possibilities for pushing any manufacturing facility towards excellence.